The granulation process of bentonite encompasses a variety of raw materials, each offering unique properties and benefits. Among these are calcium bentonite, sodium bentonite, bentonite rocks, and bentonite clay. These materials, when processed through Huaqiang's double roller granulator, transform into high-quality bentonite granules, catering to a wide array of industrial applications.

Each raw material used in the granulation process offers unique application possibilities.Calcium bentonite, for example, is commonly used in soil improvement and agricultural applications, while sodium bentonite finds significant usage in drilling fluids and construction
materials. Calcium and sodium bentonite are particularly notable for their water absorption and swelling capabilities, making them ideal for use in environmental protection, drilling fluids, and as a binding agent in foundries. Bentonite rocks and clay, on the other hand, undergo a meticulous granulation process, enhancing their utility in products such as cat litter, construction materials, and in the agricultural sector as soil conditioners. Bentonite rocks and bentonite clay have their own niche applications in various industries. Huaqiang's granulator is perfectly suited to cater to the diverse needs of different raw materials.
Huaqiang's double roller granulator stands out for its dry granulation process,eliminating the need for drying and significantly reducing energy consumption. This feature not only underscores the machine's environmental friendliness but also its cost effectiveness.Furthermore, the granulator's robust design ensures a uniform size of granules, enhancing their applicability in various industries.
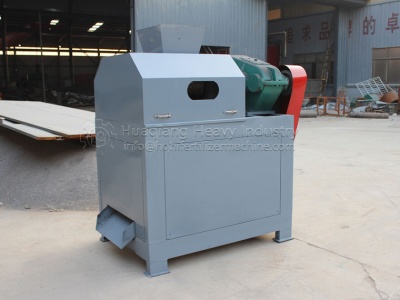
The versatility of the double roller granulator by Huaqiang allows for the accommodation of a wide range of raw materials. This adaptability ensures that clients can produce bentonite granules tailored to specific industry needs. Moreover, our engineers continuously work on refining the machine's performance, ensuring it remains at the forefront of technology, thus providing clients with a competitive edge in their respective markets.
The double roller granulator can produce finished particles ranging from 3mm to 15mm in size, catering to various market demands with specific characteristics for different materials.
Compound Fertilizer Granules - For compound fertilizers like ammonium chloride, the granulator commonly generates particles in the range of 4mm to 5mm, aligning closely with market requirements.Carbon Powder or Special Material Granules - On the other hand, materials such as carbon powder or special substances are typically be of use to form granules sized at 8mm or 10mm for optimal usability. Potash Fertilizer and lrregular Granules - For potash fertilizers and other materials not necessitating spherical particles, you can use irregular molds in production to create finished products tailored to market demands.
Firstly, the double roller granulator exhibits varying output capacities, ranging from 1-1.5 tons per hour and 1.5-2 tons per hour.Secondly, the material pelletization rate is around 90%, with compound fertilizer moisture content typically ranging from 2% to 8% and specialty materials possibly controlled below 20%.Thirdly, roller sizes vary across different machine models, such as Φ150mm*220mm with 15kW power,Φ150mm*300mm with 18.5kW power, and Φ186mm*300mm with 22kW power.Finally, the granule strength typically falls within the range of 6N to 20N (crush resistance).
.jpg)
At present, the roller socket typically features a flat-spherical shape. ln addition, the double roller extrusion granulator can accommodate a variety of ball socket shapes and sizes based on userrequirements. And, these shapes include pillow-shaped, semi-spherical, cylindrical, tablet-shaped,walnut-shaped, flat spherical, and rectangular ball sockets, among other options.