The cow dung is naturally piled up, occupying a large area, easily losing fertilizer nutrients, breeding mosquitoes and flies, and seriously polluting the environment. The application of large-scale organic fertilizer manufacturing process for cow dung can not only effectively solve the above environmental problems, but also add additional benefits for dairy farming. After many years of active exploration, Zhengzhou Tianci Company has established a set of organic fertilizer manufacturing process equipment, which can be applied to the large-scale fermentation processing of dairy cow dung, so that a large number of cow dung produced in dairy farms can be converted into high-quality organic fertilizer.
A large-scale fermentation of cow dung was established in the fermentation tank, and the aerobic fermentation technology was stirred by a semi-closed fermentation tank with continuous feeding and continuous discharging. Generally, the height of the fermentation tank does not exceed 1.5 m, and the running track of the trough compost turning machine is installed on the top surface of the groove wall on both sides of the fermentation tank, so that the configured trough compost turning machine can be operated back and forth. In the automatic forward running process, the trough turning machine is equipped with a rotating tumbling blade at the lower part to mix and stir the materials to enhance the fermentation and water evaporation. After stirring for 20 to 25 days, the fermented and decomposed materials can be transferred to the discharge port.
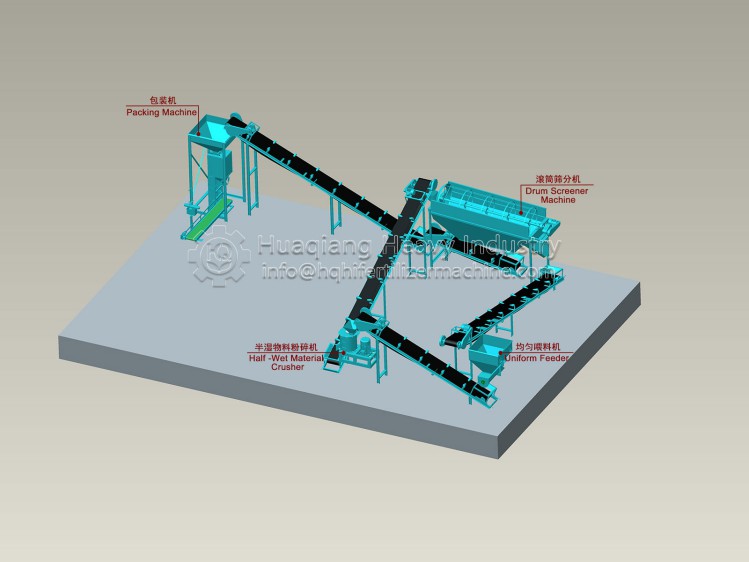
The fermented material is crushed and dispensed to the disc fertilizer granulator. Adjust the amount of material granulation water for disc fertilizer granulator, and ensure the supply of water for material granulating. The granulated material is then conveyed to the drum dryer by conveyor belt. The material is dried by low temperature hot air not higher than 40℃. The moisture content of the material after drying is less than 30%.