Before NPK fertilizer production processing, raw materials need to be crushed. Different types of inorganic fertilizer powders are proportioned, then granulated by rotary drum granulator or roller extrusion granulator. After drying and cooling system, they become finished fertilizer.
When the cage mill works, the four-layer cage bars installed on two rotors rotate at high speed in opposite direction, impacting and rolling materials. When crushing the material, the cage will also be worn out. Because of the high speed of working line, the cage is worn too fast. The medium-sized cage grinder designed by US adopts unique steel bar material. It has good wear resistance and excellent impact performance. It can ensure the normal use of grinder under different conditions. We appropriately increased the diameter of the first and second layers of cage bars to achieve uniform wear and prolong the service time of the rotor.

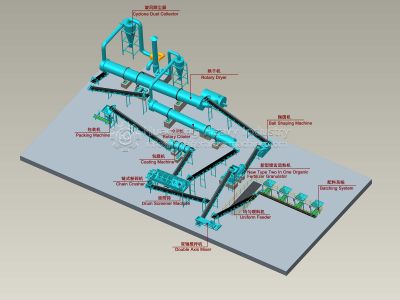
When the cage mill is running, the gap between the shell and the whole cage wheel is filled with material. The cage wheel is squeezed and rubbed by coal in the rotation, which produces greater resistance moment and increases energy consumption. Because the surface of the cage wheel and the inside of the shell are parallel, the whole area of the cage wheel is always in the process of coal extrusion and friction. Because of the large contact area, the resistance moment is large, and the non-functional consumption is increased, which affects the production capacity.
Our cage crusher has been improved to reduce the diameter of the pulley of the large cage wheel motor and its speed. The decrease of rotational speed will inevitably lead to the decrease of fineness. The cage mill has a high actual grinding fineness, which can meet the granulation fineness of NPK fertilizer production process.